Know How – Expert Edition – Braking Best Practice
25 Feb 2021
Braking Best Practice
With Graeme Ryder
Graeme is an expert in friction braking with over 20 years of engineering and automotive industry experience. Specialising in friction theory, he educates technicians at all levels in practical application and installation best practice. In this edition, Graeme highlights the important steps in achieving a problem-free brake replacement using industry best practice. If you require further technical assistance, please contact the NAPA Braking Technical Line on 0117 428 8090.
Pre-Inspection
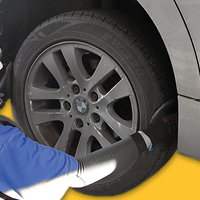
- Test drive the vehicle before removing of any parts to confirm symptoms.
- Visually inspect the tyres for uneven tyre wear, radial separation or other damage. Tyre degradation can sometimes lead to symptoms that are mistaken for brake related issues.
- Check the condition of the wheel bearings. A worn bearing can cause excessive lateral runout, which may cause the brakes to pulsate or pull.
- Examine the steering and suspension bushes and joints for any free play. Worn steering and suspension bushes will not be able to absorb vertical and lateral forces produced by the vehicle when braking and can cause juddering.
Removal
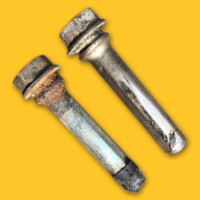
- Can the pads move freely in the caliper carrier? Corrosion build up can cause the pads to seize. *
- Are the caliper fingers and piston contact points aligned? Excessive corrosion can cause misalignment of the pads. *
- Remove the caliper to enable inspection of both caliper sliders. Deteriorated sliders and rubber boots can prevent free movement. If in doubt of their condition, these should be renewed. *
- Can the caliper pistons retract and move freely? *
- Measure the brake discs, using a micrometer. Measure in at least 8 different points at equal distance apart around the disc perimeter, 2.5mm from the outer edge. An excess of more than 0.03mm of thickness variation will result in brake torque variation and brake judder.
* Anything interrupting free movement of brake components will interrupt the even material transfer process, leading to excessive DTV eventually resulting in brake judder.
Preparation
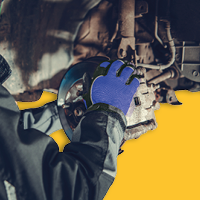
- With a tool that will not compromise the metal, remove corrosion from the caliper carrier, caliper fingers and piston contact points.**
- Inspect the hub and remove the corrosion build up using a suitable tool.**
- Treat and protect all surfaces by applying a water resistant, metal free lubricant with a high melting point.**
- Completely remove all sliders and clean thoroughly, including their cavities.
- Treat and protect sliders with a rubber compatible, water-resistant lubricant.
** Corrosion build-up alters braking component tolerances.
Fitment
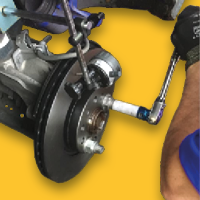
- Replace brake discs as an axle set to ensure braking consistency.
- Clean the disc and mounting surface. Dust and foreign objects trapped between the mounting surface of the disc and the hub will cause lateral runout. This can lead to disc thickness variation and brake judder.
- If the component is equipped with a disc locating screw, renew and replace as it secures the brake disc and prevents dust and debris from entering behind it.
- Mount and secure the disc and check for disc runout using a DTI gauge. This should be no greater than 0.08mm on a small/medium family car or 0.05mm on a luxury/performance car. Anything more can cause excessive lateral runout, disc variation thickness and brake judder. †
- Examine and thoroughly clean the contact surface of the wheel. Contamination or poor quality alloy wheels will cause excessive lateral runout and brake judder.
- Torque wheel bolts following in the correct sequence. Incorrect torque could damage the disc hat, distorting the hub contact surface, causing excessive lateral runout and brake judder.
† Exact vehicle manufacturer tolerances must be used. Measurements supplied are a guide.
Aftercare
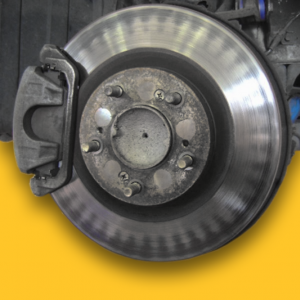
- Follow the recommended bedding-in procedure. The process will take longer for fully coated discs as the coating must be removed for the material transfer process to take effect evenly on the disc surface.
- Ensure the driver is aware of the recommended aftercare for the initial 200 miles (at least). Material transfer process can still be affected after this if using an incorrect braking technique. All NAPA discs are precision edge coated so removal is not necessary.
Become a NAPA Stockist Download PDF Guide